about us
About us
Our company
Dylco develops, produces & finishes knitted fabrics since 1957.
Located in the North of France, in one of the 3 cradles of the textile industry in the country, its influence extends on the European continent level, and further, with 75% of its business being exported.
It is above all the know-how and interdisciplinarity expertise in product development that enable Dylco to be a recognized company in the European market, and further.
Diversification has become the Dylco management’s key commitment since about 20 years to install the Company in a constant development.
What project do you want Dylco to deal with ?
Our roots
Dylco is a French industrial SME located in the North of France, dedicated to warp knitting manufacturing for about 70 years, initially for the automotive market and then rapidly a wide variety of sectors.
Dylco has been an offshoot of a textile company, a company that has been designing and producing lace for fashion and home curtains for 160 years.
Dylco has been operating as an independent company since 2021 to strengthen it capability of strategical development, with its own means and an independent management.
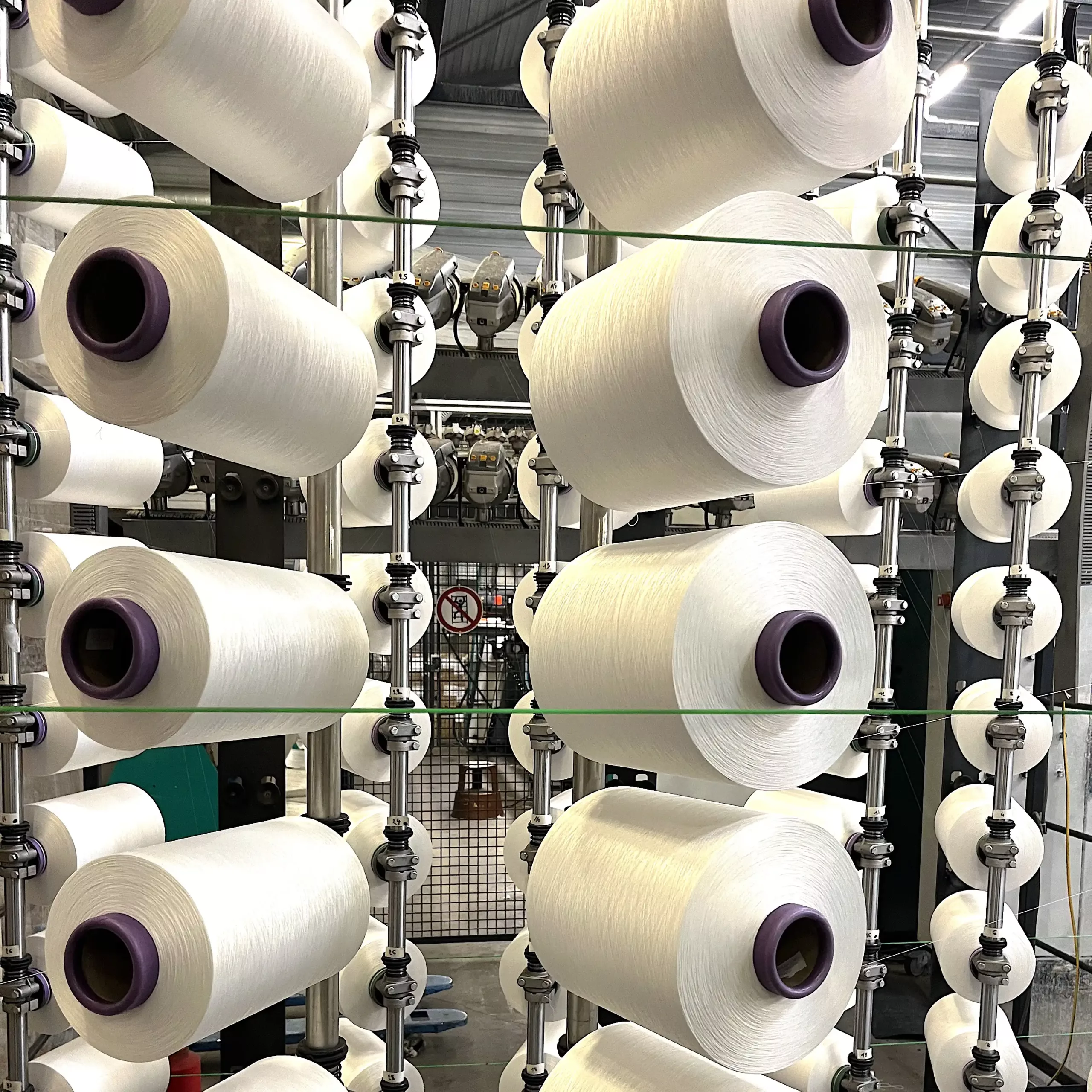

We provide individual solutions
In an intensive exchange and based on your specific requirements of the project, our team develop tailor made solutions for you.
Textiles that reliably and precisely is a technical answer within your industrial project.
We support you from the initial idea to the finished product: a high-quality textile component that – as small and hidden as it can be – often makes the decisive difference to the success of your project.
It is above all the know-how and interdisciplinarity expertise in product development that enable Dylco to be a recognized company in Europe.
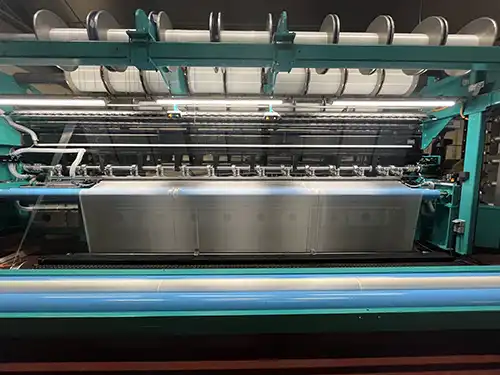
History and company development
History and company development
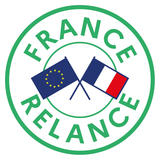
Dylco has been awarded a subvention from the French government.
applications and technology
applications and technology
Considering though orientation of the force taking yarns this fabric is comparable to a woven fabric. However, there is the advantage that yarns are directly oriented and lie absolutely straight in the fabric. This means that there is no loss of tenacity as in the woven due to its crimp effect. Furthermore, the yarn-protective inlay system prevents all fiber damage.
A one stop factory with vertical integration
Warping facilities
Warping is defined as the parallel winding of yarn from a cone onto a warp beam.
This process is necessary for the warp knitting production preparation.
2 warping facilities are part of our machine fleet.
Warp knitting facilities
Warp knitting is particularly well suited to the production of sequential lengths of fabric, composites, conveyor belts, safety clothing, advertising banners and so on.
We have several knitting machine technologies capable of meeting most of our customers’ projects.
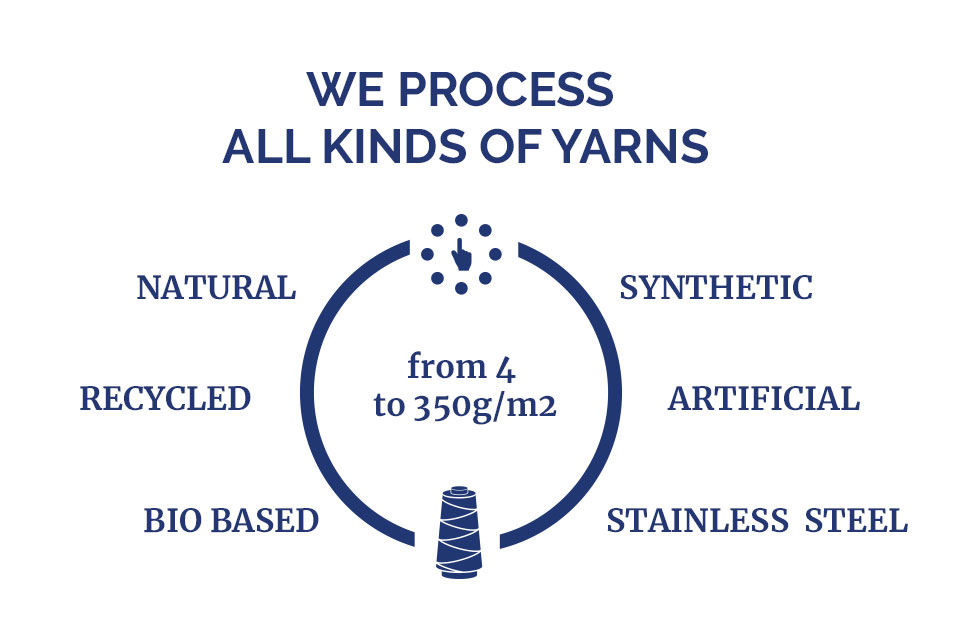
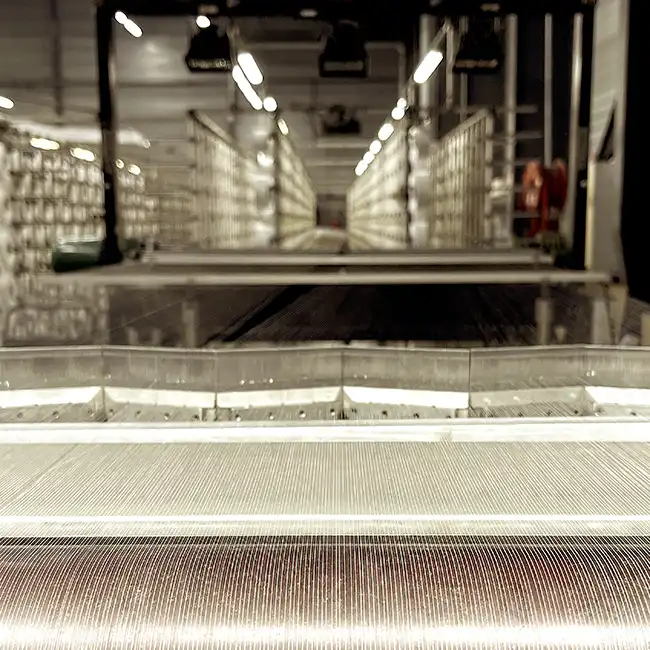
Finishing facilities
Heat-setting is a heat treatment by which shape retention, crease resistance, resilience, and elasticity are imparted to the fibers. It also brings changes in strength, stretchability, softness, dyeability, and sometimes on the color of the material.
Before conducting the fabric into the oven for heat-setting, we can add functionalities by dipping it inside a solution of various primer formulas : stiffeners, flame retardant treatments, etc.
Dyeing : flexibility is our strength
Our company has the capability to dye fabrics with Over flow and Jet HT technologies, particularly to answer the PPE market when the flexibility is necessary thanks to a low MOQ (300ml).
R&D
Our labt and the knowledge and expertise of our R&D team mean that we can assess our developments at every stage of the design process. This supervised approach saves you valuable time and increases the reliability of your certification processes.
facts and figures
facts and figures
Ladder proof fabrics (wrap knitting)
market segments
market segments
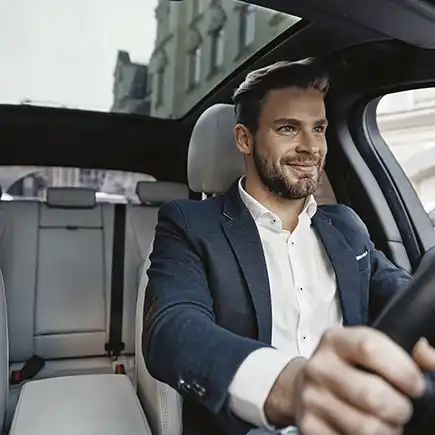
Mobiltech
- Automotive :
- Seat cover -textile & leather-
- Panel renforcement
- Camping car solutions
- Public transport
- Green mobility :
- Commuting (cycling, scooter)
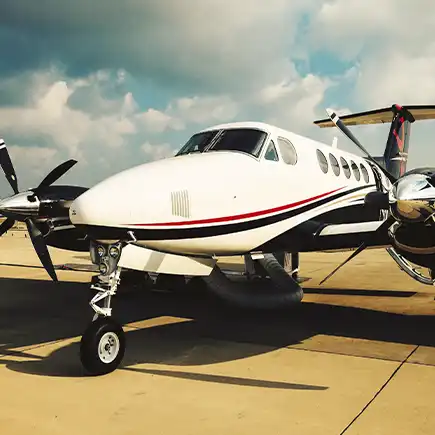
Aerotech
The aircraft constructors challenge their supply chain for textiles that are mainly used in the interior as well as in laminates in the structure that are subject to extremely high safety requirements :
• Aircraft insulation
• Wing mecahnical defrost
• Seat cover
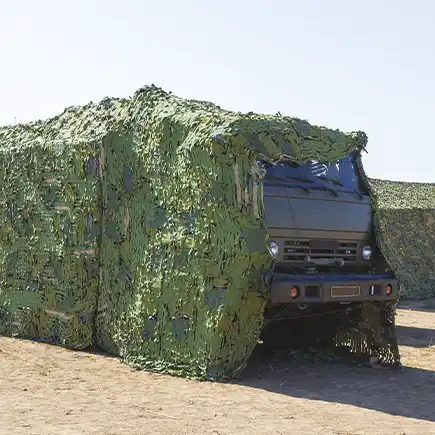
Protectech
Textiles dedicated to personal protective equipment -PPE- are highly functional and constantly evolving, with a twofold constant problem: providing both comfort and protection during operations (firefighters, military, law enforcement).
We manufacture textiles with high-tenacity technical yarns (PA 6.6) and heat- and fireresistant yarns (aramids. FR viscose, blend of both etc).
• Underwear of varying degrees of warms
• Depending on the theater of operations
• Body armor
• IR & radar camo net
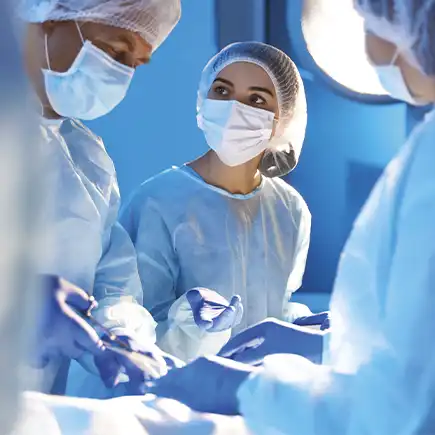
Medtech
Functional textiles for processes governed by IS013485 standard (medical devices) that are characterized by biocompatibility or materials with antibacterial properties (cf: polypropylene used for surgical implants).
• Plasters
• Trips
• Loop fabric for repositionable nappies
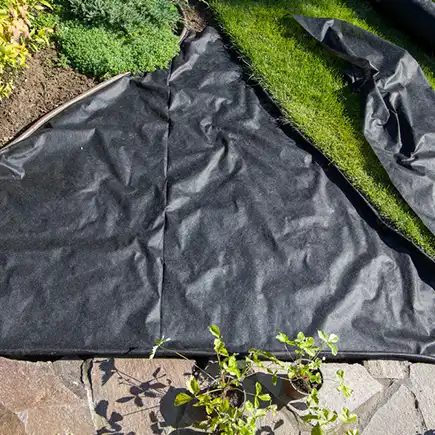
Industrytech
• Agritech
• Agrotextiles
• Construction

Hygienetech
• Pet & mosquito screens
• Flooring & roofing solutions
• Baby pushchair
market segments
market segments
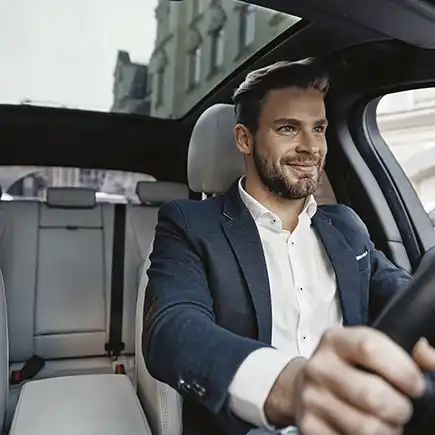
Mobiltech
- Automotive :
- Seat cover -textile & leather-
- Panel renforcement
- Camping car solutions
- Public transport
- Green mobility :
- Commuting (cycling, scooter)
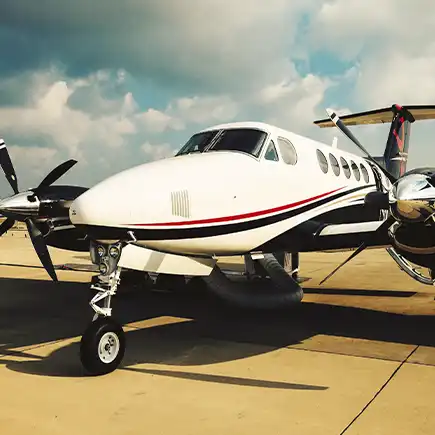
Aerotech
The aircraft constructors challenge their supply chain for textiles that are mainly used in the interior as well as in laminates in the structure that are subject to extremely high safety requirements :
• Aircraft insulation
• Wing mecahnical defrost
• Seat cover
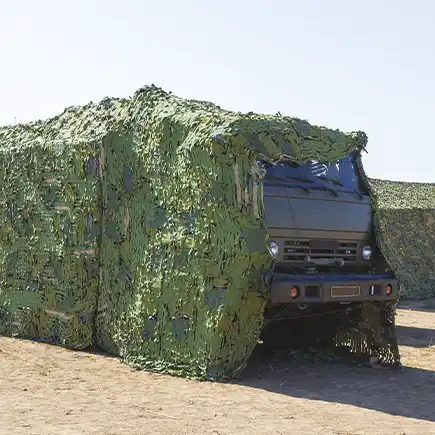
Protectech
Textiles dedicated to personal protective equipment -PPE- are highly functional and constantly evolving, with a twofold constant problem: providing both comfort and protection during operations (firefighters, military, law enforcement).
We manufacture textiles with high-tenacity technical yarns (PA 6.6) and heat- and fireresistant yarns (aramids. FR viscose, blend of both etc).
• Underwear of varying degrees of warms
• Depending on the theater of operations
• Body armor
• IR & radar camo net
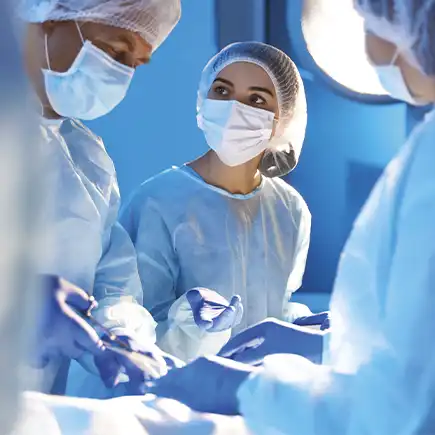
Medtech
Functional textiles for processes governed by IS013485 standard (medical devices) that are characterized by biocompatibility or materials with antibacterial properties (cf: polypropylene used for surgical implants).
• Plasters
• Trips
• Loop fabric for repositionable nappies
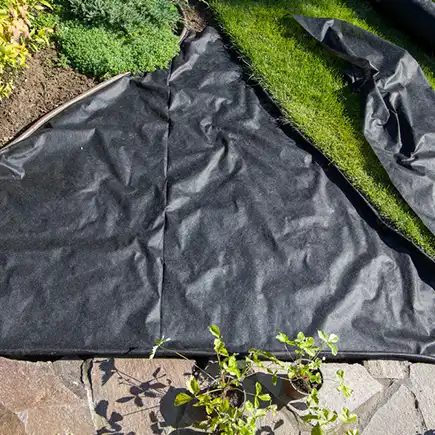
Industrytech
• Agritech
• Agrotextiles
• Construction

Hygienetech
• Pet & mosquito screens
• Flooring & roofing solutions
• Baby pushchair
values
values
Sustainability
We have set ourselves concrete and ambitious sustainability targets – in all three dimensions, social, ecological and economic. By 2035, we want our activities and the energy we use to be 70% climate-friendly on our site.
Social environment
As a company :
- We take our social responsibility very seriously ;
- The low turnover rate among our team in all existing positions since 1957 leads to a situation our management is really proud of ;
- In the Dylco Code of Conduct, we commit ourselves – all the employees of our company – to our sustainability objectives. In order to achieve our ambitious goals, we break them down into concrete, time-bound and fixed sub-steps. We set ourselves binding and verifiable standards.
Economic environment
Dylco strengthen all efforts to keep a sustainable economic environment.